Brands, retailers and manufacturers need to accurately calculate their minimum stock levels with a formula in order to effectively manage their inventory and order fulfillment - and optimize the entire supply chain.
This key figure is essential for long-term success in today's dynamic retail environment: it helps you to withstand fluctuations in demand and supply bottlenecks, and ensures operational readiness.
Careful planning of minimum stock levels is particularly important for globally active companies, as transportation distances have increased considerably in our networked, digital world.
In this guide (updated for 2025), we'll explain what a minimum stock level is, how to calculate it with a simple formula, look at the latest industry trends and more.
What Is a Minimum Stock Level?
Minimum stock, also known as safety stock or reserve stock, is the amount of stock that must always be available to ensure a company's ability to meet customer demand, even during seasonal peaks and unexpected supply issues.
It is effectively the stock reserve in your warehouse and serves as a buffer against unforeseen supply bottlenecks or increased demand. Or to put it simply: the minimum stock level is your "cushion for lean times".
>> Read our guide to Distributed Order Management <<
Why Is Minimum Stock Important?
Various scenarios can arise in which stock levels unexpectedly run low. This is because sales are not constant throughout the year, but are always subject to seasonal fluctuations.
While seasonal fluctuations are common, recent years have shown that supply and demand in e-commerce remain highly volatile, and acute supply bottlenecks are commonplace.
They can be triggered by global events such as a pandemic, or by political changes like Brexit. New trends on social platforms such as TikTok and Instagram can also lead to a sudden spike in demand for certain products.
Brands, retailers and manufacturers are then suddenly faced with the horror scenario of an out-of-stock notification, which can cause several costly consequences.
Your customers may migrate to the competition in frustration, you suffer a loss of image, your sales decline, or you might be left with goods that were reordered too late, caused by poorly planned orders.
Industry Trends in Inventory Management
The landscape of inventory management is rapidly evolving, driven by advancements in technology and data analytics. Companies are increasingly adopting sophisticated tools and strategies to optimize their minimum stock levels, ensuring they can meet customer demand while minimizing excess inventory.
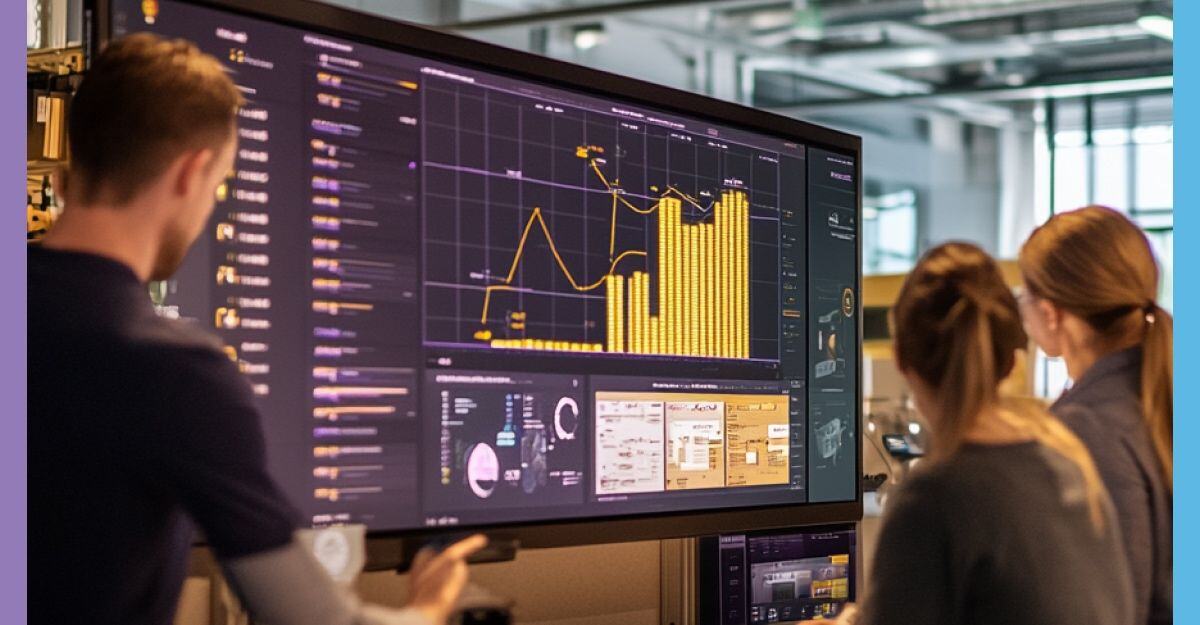
One of the most significant trends is the use of artificial intelligence (AI) and machine learning (ML) for predictive analytics. These technologies enable businesses to forecast demand more accurately by analyzing historical data, market trends, and external factors such as weather patterns and social media trends. For instance, Amazon uses AI-driven algorithms to predict demand and optimize inventory levels across its vast network of fulfillment centers.
Another emerging trend is the integration of Internet of Things (IoT) devices in supply chain management. IoT sensors can track inventory levels in real-time, providing up-to-date information that helps in maintaining optimal stock levels. Companies like Cisco and IBM are leading the way in implementing IoT solutions for inventory management, enabling businesses to respond quickly to changes in demand and supply.
Blockchain technology is also gaining traction in inventory management. It offers a transparent and secure way to track the movement of goods throughout the supply chain, ensuring that minimum stock levels are accurately maintained. Walmart, for example, has been experimenting with blockchain to enhance the traceability of its products, which in turn helps in managing inventory more effectively.
Best practices in minimum stock management include adopting a data-driven approach, leveraging automation, and fostering collaboration across the supply chain. According to a recent study by Gartner, companies that implement advanced inventory management systems can reduce their stock levels by up to 20% while improving service levels.
Minimum Stock Level Formula
The minimum stock level of a product can be calculated using a simple formula:
- Average sales per day x Delivery time in days = Minimum stock level
The delivery time in days refers to the time your supplier needs for delivery. For example, if you sell dog toys and your manufacturer normally needs 3 days for delivery, use a factor of 3 in the calculation.
Established companies can rely on historical sales data to calculate the above. Start-ups and newly founded companies, on the other hand, must first estimate their daily sales and adjust the values regularly.
For items that are less in demand, and for which no permanent supply problems or sudden increases in sales are to be expected, the above formula can be adjusted as follows:
- 1/3 x (average sales per day x delivery time in days) = Minimum stock level
Actindo Tip: Stock items will tie up your capital and cause unnecessary logistics and storage costs! You should therefore never set the reorder level too high (see explainer below).
Minimum Stock Level Example
Let's go back to the example of dog toys. Your e-commerce company sells an average of 50 units per day. The manufacturer's average delivery time is three days from receipt of the order.
Since you need to be very sure, you decide to use the formula with the complete average consumption. The minimum stock is calculated as follows:
Minimum stock = 3 days for delivery x 50 units ordered per day = 150 units
You should therefore have at least 150 dog toys in stock as a minimum. In the event of unexpectedly high orders, this minimum stock level will allow you to meet demand for at least another three days without any problems, thus ensuring a constant standard of service.
Next, you need to calculate your reorder point (ROP), so that you know when to place another order...
Minimum Stock vs. Reorder Point
While the minimum stock level represents the lower limit of the stock level, the reorder point (ROP) indicates the moment at which a reorder should be triggered in order to avoid having to use the minimum stock level.
The reorder level is therefore higher than the minimum stock level. The formula for the reorder point is based on the minimum stock level, and looks like this:
- (Sales per day x Delivery time in days) + Minimum stock level = Reorder point level
So if you sell 50 dog toys per day, and they take 3 days to be delivered, then your ROP is calculated like this:
Reorder point: (50 x 3) + (50 x 3) = 300 units
With the reorder level, you always have sufficient time to procure replenishment. Only when market fluctuations occur does the minimum stock become (very) necessary.
So once you calculate minimum stock and your reorder point, then you're done? Not quite...
Challenges of Calculating Minimum Stock Levels Manually
Rough estimates are not enough for successful e-commerce, once you have multiple sales channels, high order volumes and a broad range of product SKUs.
You would have to constantly recalculate your minimum stock levels in order to be truly prepared for eventualities such as supply bottlenecks or increased order volumes.
This can become an enormous manual effort, especially if your business sells more than just 50 dog toys a day. It quickly becomes spreadsheet overload.
That's why successful brands, retailers and manufacturers rely on scalable, composable IT systems and distributed order management to cover all processes efficiently and precisely.
>> Learn more about the benefits of Composable Commerce <<
How to Calculate Minimum Stock Levels Automatically
A future-oriented Commerce Operations Platform such as Actindo Core1 enables you to automatically calculate minimum stock levels based on data histories from all sales channels.

The integrated warehouse management module enables automated and precise calculation of minimum stock levels based on real-time data from various sales channels and stock movements.
Sales forecasts, trends analyses and delivery times are continuously updated to ensure efficient management of your stock levels. This prevents empty shelves, overstocking and optimizes your overall inventory management.
The modular MACH architecture of Actindo Core1 - consisting of microservices, API-first, cloud-native and headless components - also facilitates the connection of new sales channels. All data streams and important information are centralized in real time.
Isolated solutions are therefore a thing of the past. You get a holistic, accurate overview of all business areas to make informed decisions and orchestrate orders effectively.
Discover how Actindo Core1 can help you optimize your business processes, create seamless customer experiences and future-proof your company: